Updated in December 2024
Can you tell the minimum amount of maintenance work that a manufacturer needs to complete to keep its machines running at peak efficiency and avoid unexpected and costly downtime?
It’s a tricky question, though as a reliable machine learning services vendor, we can answer it with the help of predictive maintenance (PdM) for manufacturing. Predictive maintenance is a proactive maintenance strategy that helps manufacturers detect and solve performance equipment issues before they occur as a way to reach zero downtime and reduce maintenance costs. Leveraging machine learning in manufacturing also allows extending the equipment’s useful life and getting rid of abrupt equipment breakdowns.
Still, to know whether it’s worth implementing PdM into manufacturing, you first need to understand predictive maintenance, how it works, its trends, and real-life examples. In this article, get most of your questions answered about predictive maintenance for manufacturing equipment.
Types of maintenance in manufacturing
If you’re wondering what predictive maintenance is in manufacturing, this approach emerged back in the 1990s although it hasn’t gained immense popularity until recently. This happened because of the introduction of the Industrial Internet of Things (IIoT), Machine Learning, Big Data, and Cloud Computing, which made PdM more available and affordable to manufacturers.
Reactive maintenance
As manufacturers struggled to keep up with the roaring demand, they tried different maintenance strategies. One of them was reactive maintenance, which embodies the mindset of “don’t fix it until it’s broken,” yet it ends with an increase in unplanned maintenance and downtime.
Corrective maintenance
Here we can also speak about corrective maintenance, which idea is to identify and repair a failure so the equipment could perform as earlier. The two concepts are very similar. The only difference is that reactive maintenance is about fixing the equipment when it’s completely broken, whereas corrective maintenance means the equipment is still running but noticeably deteriorating.
Preventative maintenance
Unlike reactive or corrective maintenance, preventive maintenance allows scheduled maintenance activities to perform before the problem occurs. It increases the longevity of the equipment, but it’s also very costly. And it still doesn’t eliminate the risk of equipment or its components breaking down randomly.
Condition-based maintenance
Condition-based maintenance expects equipment monitoring, and based on the data collected, maintenance activities are performed right before the failure occurs. It’s similar to predictive maintenance, which doesn’t let equipment degrade. Based on the sensor data and trends, the latter predicts degradation and failures as early as possible to extend the equipment lifecycle.
Predictive maintenance
Industrial or manufacturing predictive maintenance seems a better solution to manufacturing companies due to its ability to minimize downtime and cut maintenance expenditure. Besides, tight deadlines and profit margins in today’s manufacturing sector made unplanned downtimes even more unwelcome.
The survey of 300 industry experts organized by Frenus GmbH Darbi College proved that 80% of the respondents consider PdM essential in the manufacturing industry. 77% of them also believe that PdM is a real need to stay competitive in today’s business environment (see more detailed results of this questionnaire below).
Recently, it is also widely discussed that AI used to predict machinery failure can enhance preventive maintenance by accurately forecasting potential issues.
How does predictive maintenance work
Basically, we can say that any industrial predictive maintenance system system is composed of four parts:
- Installed condition-monitoring sensors that gather and send further real-time performance data as well as machine health info. It’s possible due to IoT technology that combines the connection between machines, software solutions, and cloud technology
- Data collection pipeline that helps with collecting data from sensors in a raw format for further data analysis and processing
- Predictive ML models that are trained on the historical data and fed with real-time sensor data to obtain failure predictions
- Analytics and monitoring software that helps with data analysis, system events monitoring, and scheduling human-machine interactions.
In addition, there are two common approaches to predictive maintenance that manufacturing companies can choose from if they want to implement PdM:
Rule-based predictive maintenance
The idea of rule-based PdM, which is also known as condition monitoring systems, lies in relying on condition monitoring sensors. Those sensors continuously collect data about equipment and then send alerts when a specific rule has been activated, in line with predefined protocols.
A special feature of rule-based AI systems includes close cooperation between production teams, engineering, and customer service departments. This cross-department collaboration is necessary to understand the direct and indirect causes that eventually lead to equipment breakdown.
Once a manufacturer knows those causes, it can create a virtual model of its connected system where they outline the behaviors and inter-dependencies between its different IoT elements. As a result, if the temperature increases above the predefined level in a smart factory, then the system sends an alert message to the team.
From the mentioned above, rule-based PdM delivers some level of automation. However, it’s still too dependent on the team’s understanding of what components or environmental events to monitor.
Predictive maintenance with machine learning
A different approach is to build AI predictive maintenance in manufacturing based on machine learning algorithms. In this scenario, ML-based systems define their own set of rules proceeding from data inputs. They take the correct data and work based on a probabilistic approach.
Precisely, an ML model uses and learns from the data generated from IIoT sensors historically and in real-time. This way, the model knows the equipment’s normal behavior and is able to detect anomaly data and events. It also helps to find correlations and make predictions for the production team to take action timely to remove the potential defect.
Here’s one more great thing about ML-based predictive production maintenance: the model can dynamically adjust to new data and make sense of what’s happening in real time.
Don’t miss our posts on traditional ML techniques and deep learning approaches to understand how manufacturers can solve a PdM problem better.
Now let’s go deeper into why manufacturers should consider implementing predictive maintenance.
Benefits of predictive maintenance in manufacturing
The list of the benefits of PdM in manufacturing is exhaustive, so we’ll focus only on the most important:
Achieve better ROI
In the case of PdM, your return on investment (ROI) is huge. First, you save on maintenance costs since you don’t perform regular maintenance tasks that may be unnecessary. Secondly, PdM solves the problem of unplanned downtime and reduces a planned one. Repairing tasks take less time because data scientists already know where to search for faulty components and why they’ve broken down. Thirdly, manufacturers can order new parts or machinery in advance. Thus, they don’t waste time waiting for them or spend extra on stocking in case of planned maintenance.
Extend the lifespan of machinery
Deloitte states that PdM increases machine uptime by 10 to 20%. First of all, the system is tracking the asset performance, so it will notice a problem before the equipment reaches the stage of serious damage. Secondly, in PdM, the useful life of machinery is long because the equipment or its parts work out all its possible time instead of being replaced regularly (as it happens in preventive maintenance).
Reduce waste
Manufacturers can also increase their bottom line revenue by reducing waste. Sub-optimal operation (when your equipment is on the verge of breaking down) usually leads to wasteful production, such as in raw materials, energy, machine time, and labor costs. PdM can warn businesses about this issue before it even happens.
Enhance performance
PdM reduces the time needed for repair as well as the frequency of repairs in general. Therefore, manufacturing organizations can operate more efficiently. Over some time, factory conditions should improve, while equipment should break down more rarely.
Improve operator safety
Getting early warning signals about faulty equipment can prevent injuries in manufacturing. Big data analysis helps to eliminate safety risks on a daily basis, plus to identify potentially dangerous conditions by keeping track of machinery for longer periods.
Protect assets
While fixing an equipment problem, manufacturers can sometimes affect other parts of the machine. PdM can help you notice any abnormal behavior after a repair so you can solve it early.
Predictive maintenance technology trends
Like any other relatively new technology, predictive maintenance for manufacturing has caused lots of hype about its adoption. Still, there are a number of specific reasons why manufacturers are looking in the direction of PdM. Below read seven predictive maintenance technology trends in manufacturing:
1. Plug and Play technology
One of the bottlenecks for introducing advanced technologies in manufacturing, including a predictive maintenance approach, is its dependence on legacy equipment. This problem is especially relevant to large companies where much of the machinery is not equipped with connectivity to send real-time info.
We’ve been working with Intelliarts for eight years. Originally, we were reaching out just for help on the engineering side. But we found a true partner. We think of them as true members of our team, and depend on them for really the day to day of the business.
Bob Dilan
PnP (Plug and Play) devices can be an optimal solution in this case. These include ready-to-use computer equipment that can connect legacy machines to computers. As a result, PdM becomes available to manufacturers, without the need to replace older equipment. Aside from this, PnP technology doesn’t require any specific knowledge to be installed, so anyone can do it.
2. AI and machine learning
No wonder many manufacturers today choose AI and ML-based predictive maintenance over rule-based systems. The use of these emerging technologies brings lots of benefits to manufacturers, from continuous learning and performance improvements to the ability to cover more complex cases to accurate anomaly detection and early failure warnings.
In today’s manufacturing environment, the situation and type of data are changing fast. And AI and ML systems can keep up with these changes.
You might also be interested in how automotive insurance leverages AI car damage detection to automate and accelerate the assessment process, improving accuracy and reducing claim processing times.
3. Supply chain cooperation
Another popular trend is to extend predictive maintenance of machines to supply chain management, which unlocks new benefits to manufacturing companies. For one thing, PdM won’t only monitor the asset lifespan but will consider production schedules and choose the most optimal time for maintenance activities. For another, the system can help manufacturers order new parts for replacement automatically.
4. Inspection technologies
Inspection technologies, such as vibration analysis or infrared thermography, offer a thorough evaluation of equipment health. With this trend, manufacturers can early detect hidden wear and rust on machinery and so mitigate risks and prolong asset life cycles.
For example, since heat is one the earliest indicators of equipment issues, thermographic analysis using infrared scanners is becoming mainstream in manufacturing. A key advancement is thermal imaging, which uses machine learning to perform temperature checks from a safe distance.
It converts infrared measurements into detailed images, providing a clear view of equipment conditions. By implementing these inspection protocols, organizations can enhance their predictive maintenance strategies and ensure efficient operations.
5. Digital twin coupled with PdM strategy
A digital twin is becoming one more mainstream technology in the manufacturing industry, helping businesses to streamline their operations. If a manufacturer has a detailed virtual version of its company, they can test processes before their introduction, make plans about new equipment installation, and so on.
To make use of this technology to its fullest, you can combine digital twins with predictive production maintenance. For example, Tech27 tells how a digital twin paired with PdM helped to save an oil and gas production plant as much as $360,000 due to predicting a potential plant outage. The two approaches make a perfect pair when there is a target to predict and when high-quality operational data are available.
6. VR and AR
Virtual Reality (VR) and Augmented Reality (AR) are another type of innovative technologies that redefine predictive maintenance for industrial equipment. Its best use cases include immediate visualization and quick diagnostics and repair. A maintenance technician wears smart glasses or a smartphone handset and automatically “scans” the component or the equipment. If needed, they could initiate an in-situ diagnostics test, thermal image, or vibration analysis to check the equipment without the need to return to a control room.
Next to diagnostics, VR and AR are also used for personnel training, remote assistance and equipment monitoring, improved documentation and knowledge management.
7. PdM As A Service
Last but not least, PdM as a service is one more interesting trend that draws the attention of manufacturers. This hybrid approach combines the effort of a dedicated service team and software so to make PdM instantly accessible to manufacturers.
This approach is particularly valued by original equipment manufacturers. OEMs produce parts and equipment for other manufacturers while PdM as a service enables them to collect real-time data from their clients’ equipment and, thus, improve their operation.
Use cases of predictive maintenance in manufacturing
Industrial predictive maintenance is a must for those manufacturers that want their assets running smoothly and without costly downtimes. Here are the most common predictive maintenance use cases in manufacturing:
- Real-time asset monitoring: Predictive maintenance is a great way to extend the useful life of their machines. Modern plants usually have expensive equipment while PdM can optimize the use of machinery via real-time condition monitoring. For instance, a modern automotive plant uses PdM to monitor the health of its robotic arms, ensuring they operate efficiently and preventing unexpected breakdowns.
- Timely diagnostics: PdM detects and diagnoses faults early, allowing manufacturers to avoid breakdowns and idle time. In the aerospace industry, predictive maintenance systems analyze data from aircraft engines to predict potential failures, enabling timely interventions before critical issues arise.
- Maintenance cost reduction: By eliminating the need for scheduled maintenance activities, predictive maintenance reduces extra expenses. For example, a chemical processing plant can leverage PdM to schedule maintenance based on actual equipment condition, cutting down unnecessary service costs and focusing resources where they are most needed.
- Reduced waste: Predictive maintenance optimizes the use of resources, machine time, energy, and labor costs. In the food and beverage industry, PdM ensures that production lines run smoothly, minimizing waste and ensuring product quality by maintaining equipment at peak performance.
- Enhanced safety: PdM improves workplace safety by predicting and preventing equipment failures that could lead to accidents. Let’s take an oil and gas industry. To improve the operations, a PdM system can monitor drilling equipment to detect signs of wear and tear, preventing potential hazards and ensuring a safer working environment.
- Improved production quality: By maintaining equipment in optimal condition, PdM helps improve the overall quality of production. In the pharmaceutical industry, predictive maintenance ensures that manufacturing equipment produces consistent and high-quality products, adhering to strict regulatory standards.
Examples of predictive maintenance in manufacturing
Learning from peers is better than entering the uncharted waters of PdM without researching the practical experience of others. For this reason, let’s take a look at predictive maintenance in manufacturing examples of three global manufacturers that have already implemented PdM into their operations.
1. Frito-Lay
One predictive maintenance system example in machinery is Frito-Lay. PepsiCo’s subsidiary Frito-Lay has a positive experience of introducing a robust program of PdM technologies. According to its manager’s presentation at the Cascade Partners Manufacturing Report, PdM helped the company reduce planned downtime to 0.75% and unplanned one to 2.88%. The manufacturer also improved its operations in a range of ways thanks to PdM.
Specifically, the technology warned and helped to prevent the failure of a PC combustion blower motor. If the company hadn’t responded as early as it did, this failure could have caused the shutdown of the entire potato chip department for an unknown amount of time.
One more example includes the early detection of increased acid levels in oil samples, which most likely warned about oil degradation. Unless it hadn’t been fixed, this problem could have led to downtime in Cheetos Puffs production and low sales.
2. General Motors
General Motors (GM) implemented PdM using IoT sensors and AI to monitor the health of their assembly line robots. This comprehensive approach allows GM to detect early signs of equipment deterioration, thereby preventing unplanned downtime and extending the life cycle of their machinery. This system helped reduce unexpected downtime by 15% and saved the company approximately $20 million annually in maintenance costs.
One notable example is GM’s Saginaw Metal Casting Operations, where predictive maintenance has been instrumental in maintaining the efficiency of casting equipment. By leveraging these advanced technologies, GM has not only reduced maintenance costs but also improved production reliability and safety.
3. Mondi
Another interesting use case for predictive maintenance in manufacturing includes the achievements of Mondi manufacturer that produces paper and packaging products. The company has implemented PdM specifically to avoid abnormal shutdowns of its plastic extruder machine in Munich’s plant, Germany. A single failure of this equipment cost the manufacturer as much as €50,000 in cleanup and lost revenue, according to Rainer Muemmler, the speaker at PAW Industry Virtual Conference.
By estimations, the introduction of PdM allowed Mundi to save from €50,000 to 80,000 mainly due to reduced operating costs and less waste generated by the machine.
4. Ecoplant
EcoPlant assisted Israeli food companies by using predictive maintenance to optimize air compression systems, which consume up to 30% of a plant’s electricity. By implementing predictive maintenance technology, plants can monitor and manage their air compressors more efficiently. The system uses real-time data and predictive analytics to identify potential issues before they lead to equipment failure, allowing for timely interventions that prevent downtime and maintain production continuity.
If you want to read more about the nuances of PdM implementation, here’s a Predictive Maintenance case study covering a PdM machine learning solution for hydraulic systems.
How to implement a predictive maintenance strategy in the manufacturing industry
Most manufacturers may find a transition to predictive maintenance rather overwhelming. To make it smoother, follow the next strategy:
1. Analyze historical data
Before you go all in predictive maintenance, you’d better know your current state of affairs. Check your occurrences of downtime, their frequency, and scale; review defects, their types, and costs; finally, look closely at reactive and preventive maintenance activities you completed for each asset.
2. Identify priority assets
Use the insights above to get a clear understanding of the most critical assets to your operations. Your next step as a manufacturer is to install condition-monitoring devices and IoT sensors on this equipment. No need to install all available devices on the market — a thermal imagery camera, vibration meter, and oil measurement could be your starter pack.
3. Start a pilot project
The same as with assets, you don’t have to try the uncharted waters of PdM with a big and costly project. Start with less and initiate a pilot project with one or two most suitable assets and machinery.
4. Move on and scale
Once your pilot project proves successful, you’re ready to scale up the effort. The good news is that predictive maintenance in the manufacturing industry can be scaled up in quick tempos, especially if you pair up with professionals. From 6 to 12 months, your company can grow from several connected machines to a smart factory.
5. Have a detailed plan ahead
We also recommend having a clear vision of what you want to achieve. Get a detailed plan of implementation, a realistic budget and time expectations. Also, think about the goals of your PdM project, try to make them measurable, and track the progress.
6. Seek professional help
Not to waste your company’s resources, get an expert machine learning services to help your company implement PdM successfully. You can also ask experts to analyze the weak points of your PdM journey if the results of your pilot project weren’t as promising as expected.
Challenges with industrial predictive maintenance
Sure, a manufacturer could meet a range of challenges along the way to building a smart factory. Here are the key stumbling blocks to PdM:
Outdated equipment and machines
Sometimes, it happens that industrial machines are too old to be equipped with smart sensors. In this case, a manufacturer has to figure out how to make them compatible, for example, by updating or replacing the machines. This challenge particularly makes sense when considering predictive maintenance used in which phase of manufacturing, as older equipment may not be easily integrated into predictive maintenance strategies at certain stages.
Additionally, integrating new technology with legacy systems can be complex and costly, requiring custom solutions or hybrid systems that bridge the gap between old and new equipment.
Data issues
Having no experience with PdM, manufacturers might be stuck on what data to collect and how to gather and store them right. Furthermore, the quality and quantity of data are crucial; insufficient data can lead to inaccurate predictions, while poor data management can result in data silos and loss of valuable insights. Proper data governance and infrastructure are essential to leverage PdM effectively.
The lack of expertise
Manufacturers also need a tank of ML knowledge to make sense of their messy historical data; choose the most appropriate ML algorithms out of dozens available; and train and fine-tune the algorithms in the most efficient way. Partnering with a provider of technology consulting services is crucial when implementing predictive maintenance systems for manufacturing companies, as these systems require specialized expertise to properly integrate and optimize.
Besides, hiring and retaining skilled data scientists and ML engineers who can handle the complexity of PdM systems is a significant challenge, often requiring partnerships with external experts or continuous in-house training programs.
Integration with existing systems
Integrating PdM solutions with existing enterprise systems like ERP and MES can be challenging. Ensuring seamless data flow between PdM systems and other operational systems requires robust API management and interoperability standards.
Digital mindset and culture
Having the right technology isn’t enough for a manufacturer’s success. Your corporate culture should have data-driven decision-making, focus on innovative technologies, and cross-functional collaboration between the IT department and other teams, including operators on the factory floor. Staff education is an important puzzle a manufacturer has no right to ignore if they want to implement a PdM solution.
By addressing these predictive maintenance in manufacturing challenges through strategic planning, proper resource allocation, and fostering a culture of continuous improvement, manufacturers can successfully implement predictive maintenance and reap its numerous benefits.
Getting started with predictive maintenance in manufacturing
If you read this far, you probably already wonder whether and how predictive maintenance could be useful to your manufacturing organization. To research this question more thoroughly as well as to get to know how to shift to PdM smoothly, you are welcome to read our Predictive Maintenance White Paper.
Optimizing a maintenance strategy is difficult but important for manufacturers. The most reliable way to do it is to implement predictive maintenance. PdM will help you define the best time to do maintenance activities, warn you about any asset problem and potential downtime, and improve the useful life of the equipment. As industries embrace digital transformation, integrating predictive maintenance does not only become a competitive advantage but a necessity for sustainable growth.
As a manufacturing software development company, we at Intelliarts love to help companies solve the challenges with data strategy design and implementation, so if you have any questions related to Predictive Maintenance in particular or other areas of Machine Learning — feel free to reach out.
FAQ
1. What challenges should manufacturers be aware of when implementing predictive maintenance strategies?
Predictive maintenance implementation could be challenging. Keep in mind the next difficulties: the need to collect and manage massive amounts of data; the employee skill gap and, thus, the need for personnel training; privacy and security concerns.
2. What is the ROI (Return on Investment) for predictive maintenance in manufacturing?
The ROI largely depends on the plant performance, data availability, and the industry the manufacturer operates in. Still, we can say about ten times the cost on average.
3. What are some common misconceptions about predictive maintenance that manufacturers should be aware of?
Be aware of the next misconceptions about predictive maintenance: PdM is too expensive and, thus, it’s for large manufacturers only; deploying IoT sensors is enough for PdM; PdM systems are too complex; PdM is a danger to human jobs; PdM is one-size-fits-all-solution.
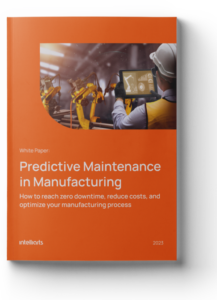