If you step inside any factory floor today, you’re unlikely to see any similarity with the leading factory of ten or even five years ago. Today’s factories are equipped with IoT devices and integrated with emerging technologies, including cloud computing, AI, and ML.
This is how industry 4.0 is paving its way for the manufacturing industry, enabling factories to collect, analyze, and make decisions based on immense stockpiles of data. But what’s the value for business owners? Increased automation, a new level of process efficiencies, and improved quality at lower costs, to name a few.
In this post, we tell about the biggest shift that hit global manufacturing since automation — the phenomenon of manufacturing 4.0, technologies, effects, who is using industry 4.0 today, and examples of smart factories in industry 4.0.
What is industry 4.0 in manufacturing?
Industry 4.0, also known as manufacturing 4.0, mixes the latest manufacturing technologies with IT, such as IoT, big data and analytics, artificial intelligence (AI), and machine learning (ML), in order to improve business processes and allow for better decision-making.
Characteristics of industry 4.0 in manufacturing
The definition of industry 4.0 is rather vague, and it’s often used interchangeably with other notions, including manufacturing 4.0, smart manufacturing, and a smart factory. It’s easier for us to define its main features to be sure you understand it right.
So, industry 4.0 in manufacturing is usually characterized by:
-
The bridging of the physical and digital world through the use of cyber-physical systems (CPS). CPS refer to intelligent physical components, objects, and software systems with embedded computing and storage capabilities. These systems form the basis of industry 4.0 and are enabled by Industrial IoT (IIoT).
-
Enhanced decision-making thanks to embedded sensors and interconnected machinery. IoT and IIoT produce lots of big data, which manufacturers can then analyze to explore historical trends, identify patterns, and use in production decision-making. A company can even build a complete virtual representation of the industrial processes and create a so-called digital twin.
-
Interconnectivity achieved by sensors, devices, and machines fully integrated into manufacturing. A smart factory means integrated operation technology with IT and, thus, smooth cooperation between the two departments.
-
Real-time monitoring, enabled by the use of IoT and IIoT again. This ensures a timely response to any changes on the factory floor and minimizes the waste of resources. Similarly, implementing IoT in solar energy applications facilitates immediate detection of performance issues, ensuring optimal energy output.
-
Decentralized manufacturing as CPS are able to decide on their own and help to perform tasks autonomously. Manufacturing 4.0 doesn’t rely on central computers or pass the decision hierarchically. Instead, it provides more flexibility to local operators and allows them to respond to changes in place.
-
Improved information transparency due to collected data from sensors. This provides a better understanding of the manufacturing processes and, thus, contributes to data-driven decisions.
-
Product customization that meets individual customer needs, yet remains cost-effective. With advanced technologies such as 3D printing, smart factories stand aside from a one-fits-all model. Instead, they could easily create more diversified goods for customers.
Every business is still unique, and even the most prominent smart manufacturing examples may have not all the characteristics described.
What technologies are driving Industry 4.0?
Let’s also take a closer look at the most important technologies that make a difference in manufacturing 4.0. Together, the five technologies from the list form a high-tech ecosystem on the factory floor and help to increase process efficiencies.
1. IoT and IIoT
IoT/ IIoT sensors are probably the most critical component of smart factories. These connect machines be
tween themselves and to the networks and provide monitoring of equipment, its components, processes, and products.
IoT/IIoT sensors are probably the most critical component of smart factories. These connect machines between themselves and to the networks and provide monitoring of equipment, its components, processes, and products.
The technology makes it possible to capture large amounts of data in real-time related to the manufacturing process. Later, this data can be analyzed to understand the behavior of the industrial environment to streamline business processes and optimize supply and demand.
2. AI and ML
Although valuable, the data received from IoT/IIoT devices is too vast for people to analyze manually. Fortunately, AI and ML algorithms are skillful enough to contextualize this info, find anomalies, and make recommendations based on this.
The most explicit smart factory example is the use of ML in predictive maintenance in manufacturing in order to detect early warning signs of equipment breakage or degradation. An ML-powered model can track and warn about temperature anomalies on the factory floor (or any other deviations). The manufacturer will then interfere timely before the real issue occurs.
3. Cloud computing
Smart manufacturing is impossible without cloud computing, which provides connectivity and integration of machines, equipment, and components. Another advantage of the cloud includes infrastructure, storage, platforms, and software applications. Cloud providers deliver them to store and manage the data received from IoT. Still, businesses don’t need to buy all this at once. They can scale their operations gradually, paying only for those resources and services they’re using.
4. Edge computing
Some issues, such as those related to safety or quality, need to be resolved immediately. So, data analysis should take place at the “edge” — where the data is created. This is possible with the use of edge computing which aims to bring computation and storage closer to the source of data.
While edge computing minimizes security risks, the manufacturer also saves itself from too much dependence on a reliable network.
5. Digital twin
Digital transformation provided by manufacturing 4.0 also gives way to digital twins — digital replicas of processes, production lines, or even the entire plant. This technology helps to improve performance and workflows on the factory floor, yet also test changes in a cost-effective manner. For instance, a manufacturer can test a new product design without actual investment in production.
What effect will industry 4.0 have on manufacturing?
Many businesses aim for easy wins for the production floor in industry 4.0 solutions, such as optimizing equipment utilization and reducing downtime. Industry 4.0 can deliver irresistible returns to manufacturers if implemented and maintained properly. Connected, smart manufacturing, enhanced by a fully automated production process, is a major return on investment.
Still, not every manufacturer is ready to venture into the upfront investment needed for launching a pilot smart factory project. If you need a couple of more reasons why a smart factory is worth investing in, here are the meaningful returns:
1. Increase in productivity
Enhanced productivity is the primary advantage of industry 4.0 in manufacturing. It’s also the major goal of smart factory projects. Manufacturers want to get rid of repetitive and tiresome tasks and use smart machines for this type of work. Meanwhile, human operators spend their time monitoring and maintaining systems only.
Altogether, this means faster, more efficient production around the clock and an increase in the production rate.
2. Quality improvements
While performance is the first and most important for manufacturers, product quality comes second. Fortunately, the 4.0 era has all chances to help you deliver better quality products. Processes get more automated while less human engagement means fewer errors. Besides, real-time monitoring, smart sensors, and AI/ML algorithms allow manufacturers to detect any quality issues and react to them quickly.
3. Enhanced customer experience
The improvements in product quality logically lead to a better customer experience. Moreover, the use of smart machines and automation technologies means that the manufacturer can produce goods faster and in more quantity. This increases the satisfaction level of customers, as they no longer face issues when the product is unavailable in the market.
Finally, manufacturing 4.0 contributes to products becoming more customized. Thanks to innovative technologies, a smart factory can mass-produce lines of personalized products. It can experiment with more designs and test them via digital twins, shorten routes between production and delivery, co-create, etc.
4. Cost-effectiveness
Another benefit of industry 4.0 that we can’t ignore is its cost-efficiency. Manufacturers should expect lower expenses with automated tasks and fewer production errors. Labor costs also decrease since manufacturers need fewer workers for everyday, repetitive tasks.
And one more thing to mention here. A more efficient production process, especially if a manufacturer enables predictive maintenance, means lower downtime and maintenance costs.
5. Better business continuity
When the equipment or its component breaks down, manufacturers need time and costs to replace or fix it. Now imagine this is a piece of very critical machinery that is experiencing issues — some industrial equipment that your plant cannot work without. So, add here the effects of downtime costs and damaged reputation as orders are canceled or delayed.
With industry 4.0, your business continuity won’t be affected this much. Industrial assets are connected and monitored in real time. So, any equipment issues are addressed immediately or, better, prevented. Advanced maintenance and monitoring capabilities can also help businesses notice patterns and insights in production, which you can then use to optimize the processes further.
6. Flexibility and agility
Automation, machine learning, big data and AI, also bring lots of flexibility to production. Now manufacturers can easily scale their production up or down depending on the seasonal demand and market fluctuations. They can also predict those chances and include or exclude new product lines, avoiding wasted resources in the future.
7. Higher competitiveness
Manufacturing 4.0 also brings more opportunities for companies to stay competitive in the market. By implementing a smart factory, a company can increase its production rates while also minimizing the wastage of materials and valuable resources. Earlier, outsourcing to cheaper regions was the only way for manufacturers to remain competitive. Now businesses can compensate for this with investments in technology.
Applications of industry 4.0 in manufacturing
As you can see, industry 4.0 is already transforming the manufacturing sector, especially when it comes to:
1. Asset tracking and optimization
With industry 4.0, manufacturers can locate and monitor equipment, its components, different machines, and work in process. IoT and IIoT devices at place help to increase visibility on the factory floor and keep track of every single stage of production. Based on the data collected, the factory can optimize its operations and improve productivity in the long run.
2. Quality management
Another important use case of industry 4.0 in manufacturing includes quality control and management. With the help of AI and ML, you can identify the parameters relevant to product quality and then monitor deviations, if any.
3. Predictive maintenance
Partly mentioned, predictive maintenance allows manufacturers to predict and prevent potential equipment problems. Manufacturers do their best to maximize production efficiency. And it’s not really efficient if you perform maintenance at scheduled intervals. The equipment might not need any intervention at this stage. Still, it’s also a poor strategy to wait until the equipment fully degrades and breaks down, and a manufacturer has to spend a fortune for its replacement or repair.
Many businesses that use industry 4.0 are leveraging these applications to enhance operational efficiency and customer satisfaction. From this perspective, weighing all the advantages and disadvantages of predictive maintenance, it seems an optimized solution, with systems being able to know about the business problem arising before it occurs. So, you could fix it early, avoid unplanned downtime, and improve equipment uptime.
Learn more about predictive maintenance in manufacturing by reading our White Paper “Turn Predictive Maintenance into a Success Story for Your Manufacturing Company”.
Real-world examples of manufacturing 4.0
Now let’s learn about industry 4.0 examples in today’s business environment and how manufacturers are reaping advantages from this.
Audi
One of great examples of real-world companies in retail using industry 4.0 is Audi. The smart manufacturing company is combining modular assembly (producing pre-assembled modules rather than individual components) with industry 4.0 in its car production. The factory relies a lot on big data, trying to make its production as data-driven and flexible as possible. It’s also implementing many other manufacturing 4.0 projects, from the application of virtual reality to AI/ML to 5G and 3D printing.
What differentiates Audi from other industry 4.0 companies is its focus on employees. While most companies see innovation and profitability as the main motivations behind emerging technology adoption, Audi pays much attention to the value that intelligent machines bring to the workplace. In particular, the company refers to better working conditions, especially when it comes to safety and security, improved reliability and ergonomics. As Henning Löser, Head of Production Labs, puts it:
“At the end of the day, vehicle construction remains craftsmanship. In the future, too, it will always be a question of cooperation between man and machine.”
The car manufacturer is definitely transitioning to the production of the future. Just check its fascinating use of technology in the video:
Whirlpool
The appliance manufacturer, Whirpool, introduced a powerful analytics system a couple of years ago. The company was planning to eliminate waste that was sent to landfills. In this real-life case study of industry 4.0, ML technology has helped the company to monitor the amount of wastage produced by its factories, as well as the usage of resources like electricity or water.
Whirpool’s smart factory is also a vivid example of how to connect plants distributed across the globe. IoT technology and analytics help the manufacturer monitor its sustainability performance in every plant, aiming at some unity in its zero-wastage policy.By 2023, the company has already achieved some impressive results:
- Three Brazilian plants have reached the zero-wastage goal, and what’s more, it happened two years earlier than planned. A few other facilities are also close to this goal.
- By projections, smart factories should help Whirlpool save around $1 million over the next three years,
- In the long run, the company expects to achieve its sustainability strategy with the aid of emerging technologies.
Appliance Manufacturer
In our portfolio, we have a compelling case story when we collaborated with a global appliance manufacturer also transitioning to industry 4.0. The company reached out to us for a technological solution for repeated and costly equipment breakdowns, which caused inconsistent work in the production line, delays in shipping, and overall low plant productivity.
After implementing an ML-based predictive maintenance solution, the Intelliarts team helped the company predict repeated system failures ahead of time with 90% accuracy. More importantly, this allowed the manufacturer to cut maintenance costs by 5%.
As part of the full-cycle project, we also set up the monitoring system so the customer was able to track the ML model performance and retrain it in case of any data changes. We also joined efforts with the company’s management to organize workshops for the manufacturing operators and teach them how to use the predictive maintenance solution to its full potential.
Siemens
In 2018, Siemens received the industry 4.0 award for its manufacturing 4.0 solutions implemented in Elektronikwerk in Amberg (EWA), the smart factory in Germany. Equipped with AI/ML technology, lightweight robots, digital twins for production and quality control, and 3D printing, the electronics plant has people, machines, and equipment working side by side as a single mechanism.
The smart factory uses dashboards to track machine performance and product quality in real-time, so the workers could react quickly to any deviations. Overall, different industry 4.0 components help the company increase productivity, achieve a higher degree of flexibility, and reliability.
Johnson & Johnson DePuy Synthes
Among other smart factory companies, Johnson & Johnson DePuy Synthes amazes with flexibility. While it’s challenging enough to build a factory of the future from scratch, it’s close to impossible to transform an old-fashioned factory into smart manufacturing. But this is exactly what the Irish medical device manufacturer was able to do.
By adopting IIoT and other popular technologies, DePuy Synthes created a visual factory solution, which provides real-time updates on production goals and allows factory personnel to monitor production levels. As the company’s leadership describes it, they allowed old machines to talk to each other and, as a consequence, were able to achieve a 10% reduction in operation costs and a 5% drop in downtime.
IoT and equipment monitoring aren’t the only implementations on DePuy Synthes’ factory floor. The company also benefits from 3D printing, digital twins, and AI to get advanced machine insights and optimize production processes.
Amazon
Offering technology services itself, Amazon as one of the largest retailers in the US knows how to stay at the forefront of digital technologies and built a smart factory. The introduction of warehouse robots was among its boldest innovations. The company bought thousands of robots and delegated a large part of repeated tasks to them, from carrying pods to lifting totes to packing orders for shipment.
Another interesting example is the use of predictive maintenance on Amazon’s factory floor. With the help of IIoT and machine learning, the company monitors temperature and vibration levels every hour, knowing about and eliminating potential failures almost immediately. By estimations, it has reduced unplanned downtime by 69% and saved $22.75 million since implementing this technology.
Tesla
Smart factories are especially popular among car manufacturers, but Tesla’s Gigafactory stands out even in this case. Ignoring its huge sizes (wait a minute, Nevada’s factory is 5.4 million square feet), Tesla impresses with its use of innovative technologies. Let’s take some of the most interesting examples:
- Model 3 production infrastructure has cars that can self-diagnose themselves, search for internal issues, and order replacement parts.
- Instead of a conveyor belt, Tesla uses its own invention “smart carts”. These are cart-like robots that carry individual cars and move them inside the factory.
- Shanghai’s version of Gigafactory benefits from 300 different types of robots used to automate various assembly line tasks, including narrow and deep laser welding. With this approach, factory workers don’t suffer from any harmful X-ray, while Tesla wins on welds of high-level quality.
- Tesla takes full advantage of cloud computing to store, process, and back up volumes of data collected. The company has also introduced its own Tesla Cloud. Although still under-developed and under-researched, it makes Tesla’s cars beat the competition by, for example, allowing seats and mirrors to be automatically adjusted while car sharing.
Tesla’s Smart Cart. Image taken from: US Today News
Manufacturing company
A large manufacturing company (under NDA) that we cooperated with has contacted us to solve the problem of repeated malfunctioning of the specific components of its hydraulic system. Of course, the industry 4.0 approach fitted best here.
The Intelliarts team has built an ML-based solution to predict the equipment failure of the components of the hydraulic system, prevent it from happening, and provide the proper maintenance to the facility. The customer was totally satisfied with the outcomes, with the ML models being almost 100% accurate in their results and predicting failure right. This helped the manufacturer to achieve a lower probability of unexpected downtime by the hydraulic system and, thus improve maintenance.
Read the full case study on predictive maintenance to get to know how the solution was built.
Why does industry 4.0 define the future of manufacturing?
Although some manufacturers are still hesitating to adopt innovative technologies, it’s obvious industry 4.0 and smart factories are the new normal in manufacturing. And those who transfer to manufacturing 4.0 earlier have a high chance to be ahead of the competition, let alone leveraging multiple benefits that industry 4.0 brings to manufacturing:
-
Better productivity
-
Improved product quality
-
Reduced costs
-
Increased resource utilization
-
And others
If you want to give it a try, but still don’t know where to start, our advice is to start small by equipping your factory with IoT devices and introducing basic automation. In case you already have some IoT in place and would like to use it to your full advantage, we’d recommend scaling up with data analytics and AI/ML technology. Reach us to our Intelliarts team to discover how to move to data-driven decision-making in the most effective way.
FAQ
1. What is the future of Industry 4.0?
According to McKinsey, the expected growth of Industry 4.0 is $3.7 trillion by 2025. So, the tendency is projected to gain momentum even further, bringing intensive growth and development to those manufacturers that adopt emerging technologies.
2. Can small and medium-sized enterprises (SMEs) adopt Manufacturing 4.0?
Sure. Manufacturing 4.0 has no limits when it comes to company size. By contrast, it’ll bring an extra competitive advantage to small and medium-sized businesses, helping them with more acknowledged use of resources, lower maintenance and operational costs, and quicker tempos of production.
3. What are the challenges in implementing Manufacturing 4.0?
The challenges of Manufacturing 4.0 include concerns around cybersecurity and data privacy, lack of appropriate digital infrastructure, the skill gap and labor shortages, and scalability issues, especially related to data growth.
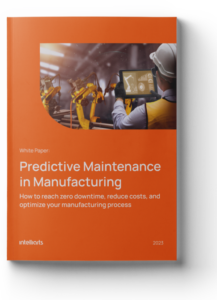