White Paper: Predictive Maintenance in Manufacturing — Everything You Need to Know
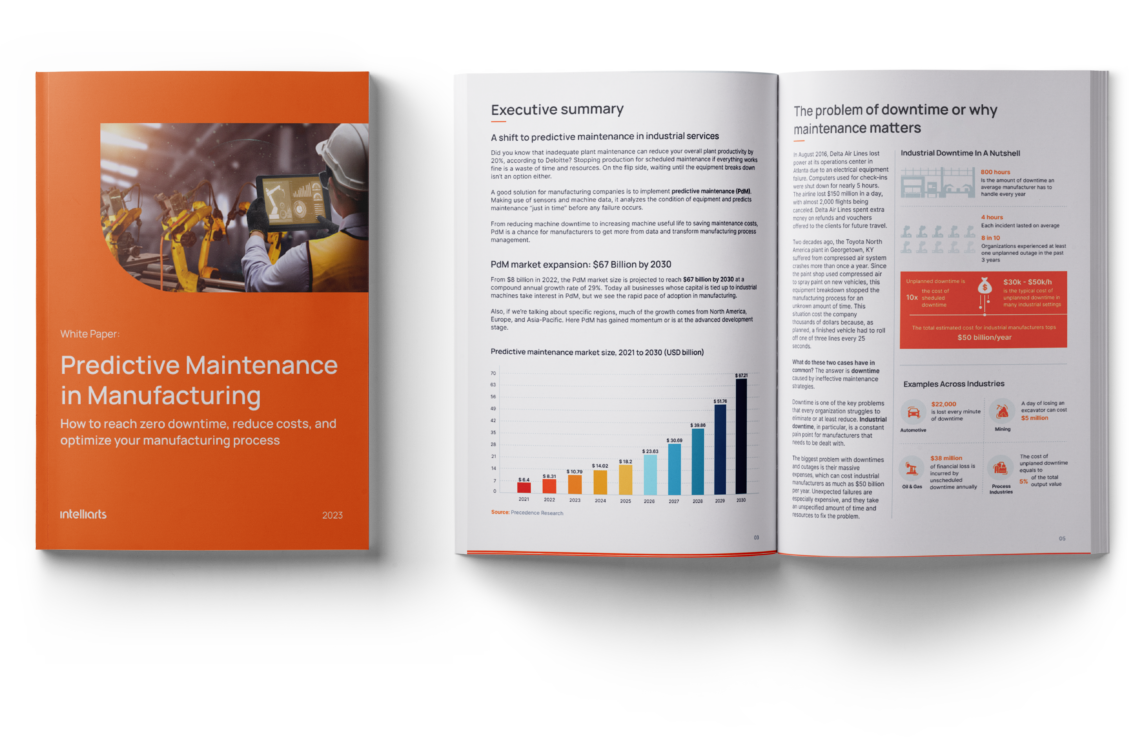
Learn how predictive maintenance can help you reduce machine downtime by at least 50% while lowering maintenance costs and increasing ROI and productivity.
The Predictive Maintenance White Paper accumulates the knowledge and expertise gained by Intelliarts’ data scientists through their work on various predictive maintenance projects.
Read it to get a chance to:
- Explore what is predictive maintenance and how to implement it right
- Contrast predictive maintenance to traditional maintenance approaches
- Discover predictive maintenance pros and cons
- See how predictive maintenance fits into your Asset Performance Management
- Check two real-life use cases of how Intellirts built predictive maintenance solutions
FAQ
What is predictive maintenance in manufacturing?
Predictive maintenance in manufacturing helps to reduce downtimes and cut maintenance costs. Based on the data collected from sensors, a predictive maintenance system monitors and analyzes equipment and identifies patterns that can potentially cause equipment failures.
What is predictive maintenance in ML?
Taking historical data and working based on a probabilistic approach, ML-based predictive maintenance solutions define their own set of rules, according to which PdM systems generate outcomes about equipment state and send notifications to the personnel.
What is the difference between preventive and predictive maintenance?
Unlike preventive maintenance, predictive maintenance doesn’t intend to take maintenance activities on a regular basis. It monitors the equipment state and suggests any maintenance steps only if the equipment or its parts are going to degrade. This way, manufacturers can avoid unnecessary maintenance and costly downtimes.